Flexibility • Scalability • Experience • Precision • Dedication • Customization
AGA’s shop fabricates and prepares a wide range of construction-ready curtainwall systems for builds ranging from historical renovations to the modern life sciences campuses. Local jobs to unique projects with one-of-a-kind architect perspectives.
We’re proud to have a flexible and dedicated in-house shop team that adapts in real time to bring the project’s vision to life. If a project plan changes, AGA is quickly able to adapt current sequencing plans to match the project timeline.
Your vision. Engineered.
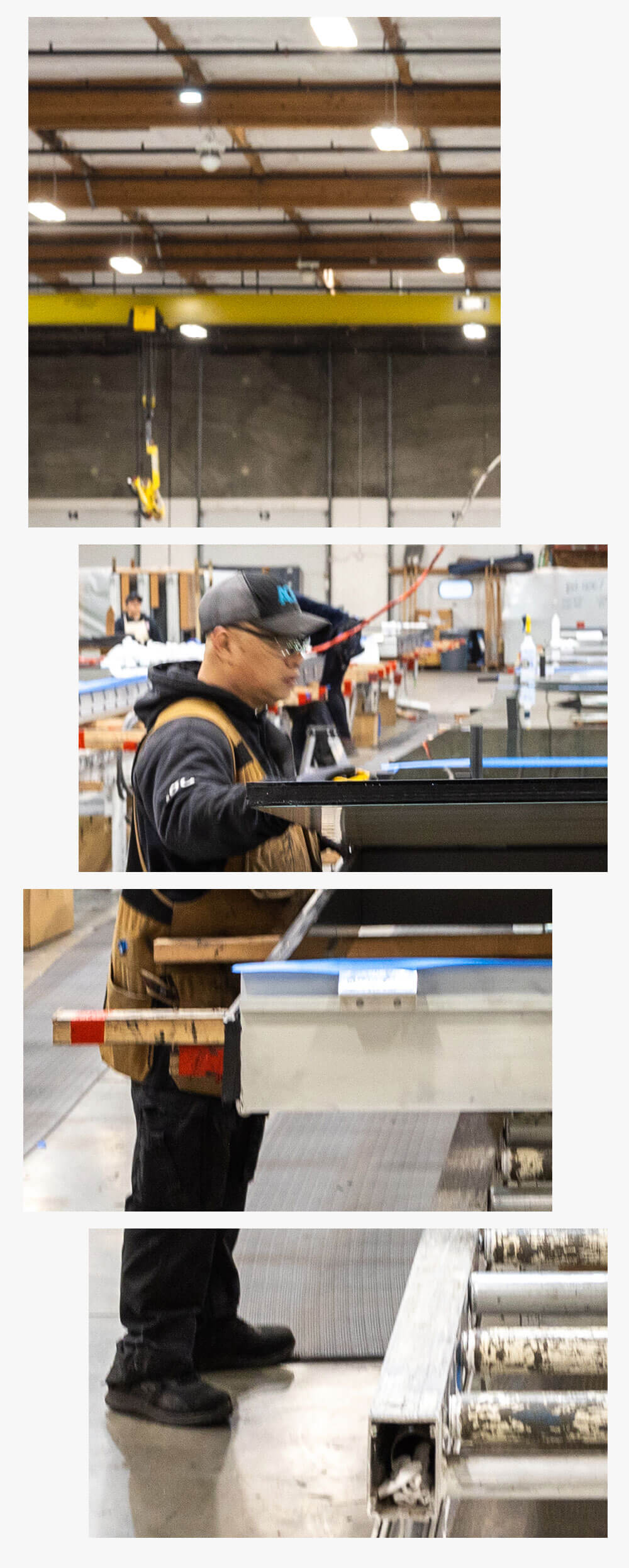
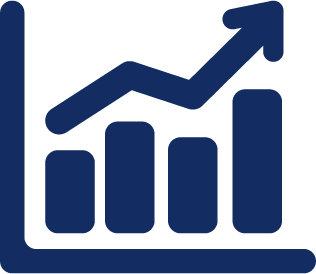
The AGA shop headquarters includes 150,000 sq. ft. of enclosed work space on 10 acres — providing the ability to handle jobs of any size.
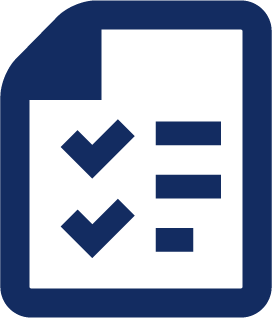
Change is a part of every job and a key reason why tracking materials, organized systems, and adaptable assembly lines are critical. The shop teams in Northern and Southern California handle the ebbs and flows of projects by embracing a fluid workflow to take advantage of having shops that are always a drive away — never a flight or ocean away.
As a North American Contractor Certified company (NACC), AGA continuously works towards improvement.

Project Engineers, Design Engineers, Shop Team and AGA team members work a stone’s throw from each other. The collaboration facilitates the project vision and maintains high project standards.
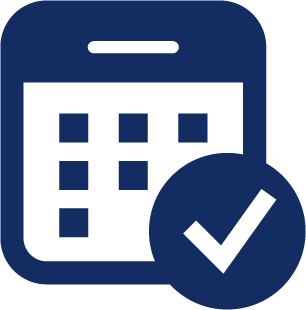
For projects with limited space on site, units are stored at AGA’s shop and delivered to a project as needed to streamline field logistics.
Seeing is Believing
Our shop team is dedicated to quality assurance.
Want to be assured our standards are as high as yours?
Schedule a shop tour and ensure the materials are part of your vision.
Creative problem solving in the shop facilitates collaboration, innovation and leads to developing new systems or evolving existing systems to fit the scope of a new project. When proofing a new concept, the shop team utilizes table top mock-up testing for mitigating water, air, and other variables.
Systems Perfected Over Time
- Proprietary quality assurance processes and punch lists
- Two Barcoding systems to track each unit’s tracking inventory and workflow
- Manufacturing peer reviews on all fabrication drawings before hitting the shop floor
High Safety = Lower Costs
Our dedicated safety team keeps the shop trained to safely operate equipment such as shop jib cranes, forklifts, and electric pallet jacks.
To further keep our team safely engaged on your job, there are regular equipment inspections and weekly safety meetings.
How else do we keep our team safe to keep your project on time? Find out on our safety page.
Pre-extrusion 3D Printing
Faster. Cheaper. More precise.
AGA’s 3D lab — located just off the shop floor — provides the opportunity to see (and feel) what components, connections and extrusions will look like before the costly effort of extruding thousands of pounds of aluminum.
3D printed versions of extrusions give architects early access to visual mockups of their projects. This helps us ensure we are on the right track to flawlessly execute the architect’s vision.